The solar battery automatic welding machine (as shown in Figure 1) can automatically and continuously weld the front and back of the battery sheet at the same time according to the set requirements to form a battery string. The ribbon is automatically fed and cut during welding, and the battery string is automatically received after welding. Welding methods include infrared lamp welding and high-frequency electromagnetic induction welding.
Compared with manual welding, automatic serial welding machine and automatic single-chip welding machine have the following advantages:
①The welding speed is fast, the quality consistency is good, the surface is beautiful, and there is no uneven soldering phenomenon caused by manual welding. Equipment welding can avoid the influence of various human factors during manual welding, such as the influence of operator proficiency, physical condition, emotional influence, etc., so as to ensure the consistency and reliability of welding.
110/220V MMA/STICK Welding Machine JARI MMA135 E
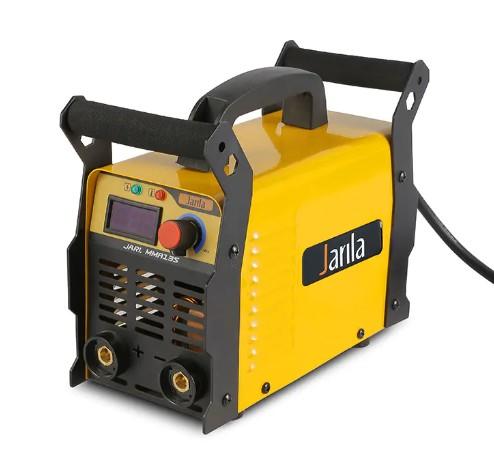
②It can reduce the number of operators and inspectors, reduce management difficulty and product cost. Now the labor cost is increasing year by year, and the annual recruitment is the most troublesome thing for the boss. The automatic welding machine can greatly reduce the number of employees.
③The welding reliability of the stringer is far greater than that of manual welding. Poor soldering is a significant cause of premature component failure. The design life of solar photovoltaic modules is 25 years, and the modules are usually installed outdoors, and they have to withstand a temperature change of about 30°C every day. Coupled with the change of seasons, the temperature change is even greater. Since the base material of the ribbon is pure copper, the expansion coefficient of copper is about six times that of silicon (cell), this difference means that as long as there is a temperature change, the soldering point between the ribbon and the battery will be stressed. Therefore, bad soldering will lead to a reduction in component power, and in severe cases, it will lead to component failure. There are many reasons for poor soldering caused by manual soldering, such as the temperature of the soldering station, the coating of flux, the temperature of the electric soldering iron, the proficiency of personnel, etc. Some aspects can be solved through effective management, while some cases cannot Fully controlled, fully automatic stringer can well solve the factors that affect welding reliability in the manual welding process.