(1) The amount of heat input can be reduced to the minimum, the metallographic change range of the heat-affected zone is small, and the deformation caused by heat conduction is also the lowest.
(2) The welding process parameters of 32mm plate thickness single-pass welding have passed the verification, which can reduce the time required for thick plate welding and even save the use of filler metal.
(3) There is no need to use electrodes, and there is no concern about electrode contamination or damage. And because it does not belong to the contact welding process, the wear and deformation of the machine tools can be minimized.
230V 5kg Car Battery Charger GZL-30
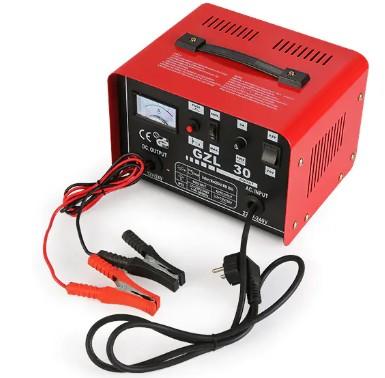
(4) The laser beam is easy to focus, align and be guided by optical instruments, and can be placed at an appropriate distance from the workpiece, and can be redirected between the machines or obstacles around the workpiece. Other welding methods are limited by the above space and unable to perform.
(5) The workpiece can be placed in a closed space (by vacuum or the internal gas environment is under control).
(6) The laser beam can be focused on a small area, and small and closely spaced components can be welded.
(7) The range of weldable materials is wide, and various heterogeneous materials can also be joined to each other.
(8) It is easy to perform high-speed welding with automation, and it can also be controlled by digital or computer.
(9) When welding thin or thin-diameter wires, there is no trouble of melting back like arc welding.
(10) It is not affected by the magnetic field (arc welding and electron beam welding are easy), and can accurately align the weldment.
(11) Two metals with different physical properties (such as different resistance) can be welded.
(12) No vacuum or X-ray protection is required.
(13) If perforated welding is used, the depth-to-width ratio of the weld bead can reach 10:1.
(14) The device can be switched to transmit the laser beam to multiple workstations.